Engineering & CAE
Mit Virtual Molding und FE-Analysen schnell und sicher von der Idee zur Serie
Im permanenten „Time-to-Market“-Wettrennen werden Produktlebenszyklen und damit auch Produktentwicklungszyklen immer kürzer. Traditionelle Produktentwicklung stösst hier an ihre Grenzen - oft verbunden mit teuren und langwierigen Anpassungen in den späteren Projektphasen. Die Folge: nicht eingehaltene Termine, ungeplante Kosten und unzufriedene Kunden. Der Einsatz von CAE ermöglicht es einen Grossteil der Produktentwicklung virtuell zu realisieren und deutlich schneller zu besseren Produkten zu gelangen. Die Grossteil Simulation erkennt früh neuralgische Stellen im Design und ermöglicht so einen reduzierten Materialeinsatz und eine belastungs- und werkzeuggerechte Konstruktion. Teure Änderungsschleifen in einer späten Projektphase können so verhindert werden.
Fehlerverhütung statt Fehlerentdeckung
Wie deutlich die Kostenreduzierung ausfallen kann, zeigt sich in der Zehnerregel der Fehlerkosten („Rule of Ten“). Sie definiert, dass sich die Kosten für einen unentdeckten Fehler pro Wertschöpfungsstufe um den Faktor 10 erhöhen. Das bedeutet im Umkehrschluss: Eine durch Computer-Aided Engineering (CAE) bestens unterstützte Entwicklungsphase spart Kosten, da Fehler schneller in der Wertschöpfungskette entdeckt und beseitigt werden können. Im Fokus steht immer die Fehlerverhütung und nicht die Fehlerentdeckung im späteren Projektstadium.
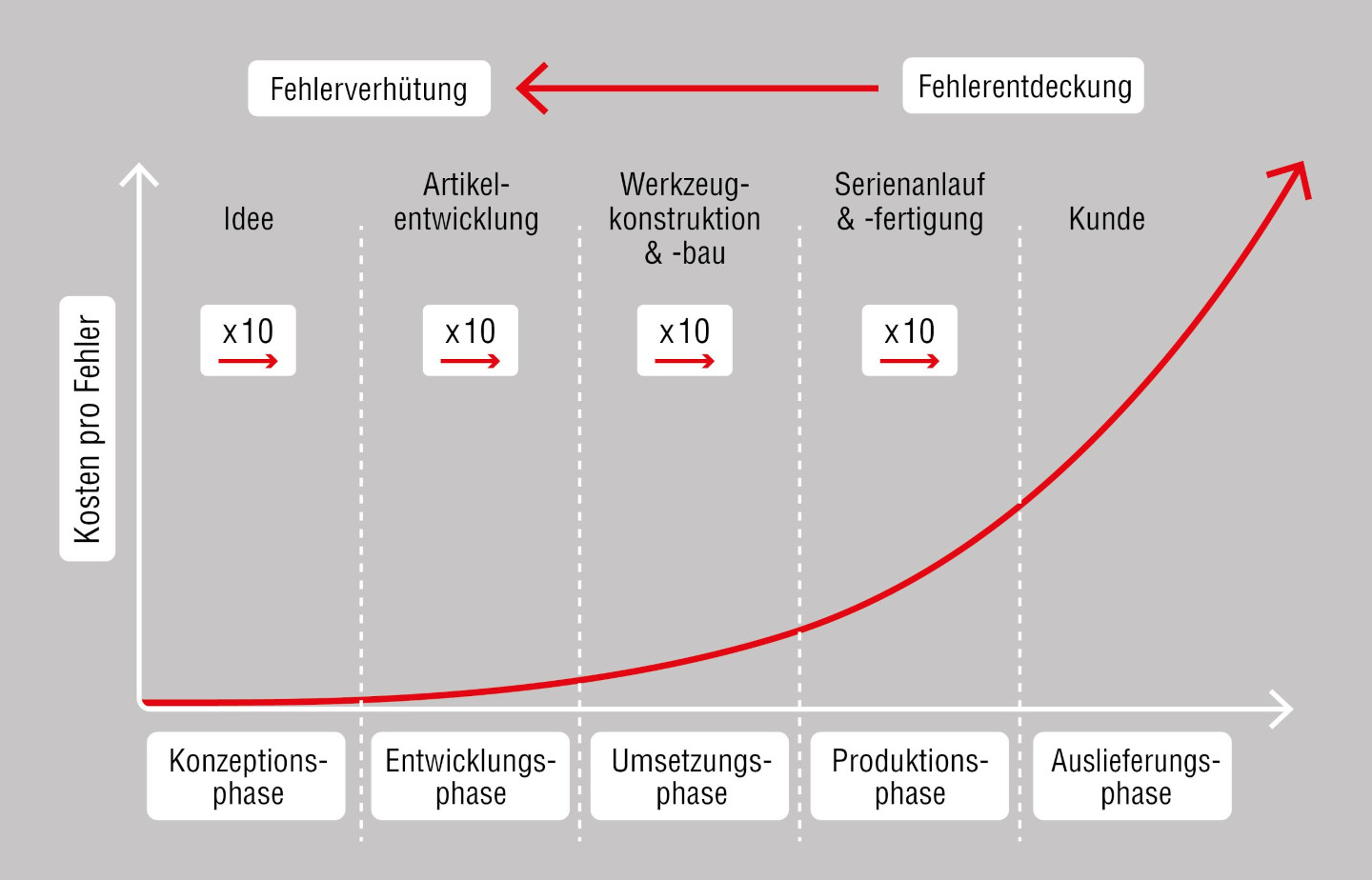